Ackerman Steering Geometry Mechanism
- Rohit Chaubal
- Aug 2, 2023
- 10 min read
Ackerman Steering Geometry Mechanism

In order for a car to turn smoothly, the inside wheel must travel on a smaller radii arc than the outer wheel allowing the car to turn. This is achieved by the inside wheel turning more than the outside wheel. This concept is known as Ackermann steering geometry.
Perfect Ackermann geometry can be devised using the wheel base of a car and knowing the the location of the lower wishbone hub pick up point. A line can then be traced from the lower wishbone pick up point to the centre of the rear driveline. The diagram below shows these lines drawn on a vehicle layout. If the tie rods of the car are placed upon this line, the car will have perfect Ackermann geometry allowing the car to turn on a very smooth arc without scrubbing the tyres.

The main purpose of a perfect Ackermann system is to reduce tyre scrub when cornering by making the inside wheel turn on a tighter radius than the outer wheel. Without this the inside tyre would have too much slip angle to turn and would be forced to give way by scrubbing the tyre. The tyre scrub effectively slows the car down and reduces grip in the scrubbing tyre.
The Effects Of Tyre Characteristics on Ackermann Geometry
Ackermann was designed for low speed manoeuvres, the introduction of Ackermann geometry into high speed situations such as Motorsport created problems with tyre temperatures and grip levels. These issues occurred due to tyre slip angles. When a car is moving at high velocity racing speeds, the Ackermann angle in the steering system is affected heavily by the tyre slip angles, often with a much lesser Ackermann angle shown between the two contact patches of the tyre.
When observing the slip angle vs lateral force curve for a racing tyre, the differential between the lateral load and the slip angle is a measure of the responsiveness of the tyre to steering inputs. The larger the differential, the less responsive the tyre is to steering inputs. As the graph in the “slip angles” section shows, as normal force increases so does the gradient of the slip angle curve giving a higher differential. This directly relates to a high speed cornering situation where the outside tyre exhibits a large proportion of normal force and the inside tyre experiences a much lower amount of normal force.
Whilst cornering, optimum slip angle must be achieved. So during a high speed corner it is possible for the outer wheel to take 75% of the normal load and the inside wheel to take 25% of the normal load. The optimum slip angle of the tyre also must be achieved at both wheels to generate maximum grip from the tyres. Often at lower normal forces, the optimum slip angle for the tyre is a smaller number. This suggests that the inner wheel requires less steering angle than the outside wheel to achieve optimum slip angle. The resulting geometry caused by the slip angle theory is often parallel or anti-Ackermann geometry.
On the other hand, some tyres show data the opposite to this suggesting that at a lower normal load, the slip angle needs to increase to obtain maximum lateral force which would suggest that positive Ackermann should be tuned into the steering geometry. Therefore, a thorough understanding of the tyre dynamics is highly important in order to correctly design the Ackermann geometry for the car.
Turning the inside wheel past its optimum slip angle will also cause the tyre to start scrubbing which will increase the inside tyre temperature and induce understeer into the car.
Aerodynamics and Ackermann Geometry
Ackermann geometry can be influenced by the aerodynamics on a car and it can influence the airflow around a car. These reasons more recently have been determining and selecting factors for Ackermann geometry within Motorsport.
With increased downforce from wings and under body aero, the lateral load transfer around high velocity corners has been rapidly reduced. This has changed the tyre dynamics during cornering and has altered the optimum operating slip angles for tyres. Due to this one of the reasons for justifying anti-Ackermann within motorsport has been ruled out as the new slip angles work in favour of a range for parallel Ackermann to positive Ackermann geometry for the optimum grip levels.
The way in which Ackermann can affect airflow around a car works at both high speed cornering and low speed cornering. During high speed cornering, if the inside wheel has more lock (positive Ackermann) then it can deflect the air away from side pods, air inlets and wings that could be fundamental to the performance of the car. Therefore sacrifice of some front end grip might be done to improve airflow. With relation to slow speed cornering, if the inside or outside wheel has a high amount of lock then it could possibly act as an air dam to the side pod or air inlet situated behind it. This problem is solved by the use of parallel Ackermann.
Pneumatic tires always roll with slip unless traveling straight ahead with their loaded rolling radius coinciding with their effective radius – an infrequent circumstance. Slippage in the contact patch is further exacerbated by vehicle braking, driving and/or cornering. Even tires rolling and turning at low speed on a dry surface will undergo overall longitudinal slip and lateral scrubbing coupled with individual tread element squirm. Such relative motion between tires and roads promotes tread wear. To help minimize unnecessary tire sliding during vehicle cornering, a four-bar linkage with an isosceles trapezoid planform, or Ackermann geometry, is generally used as the foundation for front-wheel steering control. Most road car steering is based on this layout; this also provides a symmetric response for both left- and right-hand turns.
The story of Ackermann steering begins with a rough sketch in an obscure note written by Erasmus Darwin (1731-1802) to James Watt (1736-1819) in 1767, depicting carriage wheels and axles. Darwin was an English physician with an interest in mechanical inventions (and best known today as the grandfather of Charles Darwin) and Watt was a well-known Scottish inventor.
Recall that the Ackermann principle is based only on geometry: if the inside wheel on a front axle turns through a greater angle than the outside wheel, both wheels can be made to track around a common center determined solely by wheelbase and radius. On vehicles equipped with pneumatic tires, a common turn center minimizes tire scrub and steering effort. This concept, the kinematics of steering, was captured in Darwin’s sketch 253 years ago for a horse-drawn carriage featuring axletrees paired with wooden wheels – though Darwin did not secure a patent.
The idea was independently reinvented by Georg Lankensperger (1779-1847) in Munich almost a half-century later in 1816. Lankensperger was a wagon maker, wheelwright and inventor who built coaches and sleighs for the Bavarian court.
Rudolph Ackermann (1764-1834), his German-born agent living in London, filed for a British patent (GB 4212) in 1818. Although Lankensperger was named as the inventor in the text, his contribution has been mostly forgotten.
The main drawback of pure Ackermann steering for today’s automobiles is that its premise is based on low-speed turning – quasistatic motion. Traversing a curve during moderate- or high-speed driving produces a centrifugal force that is balanced by a cornering force acting on each tire. These equilibrating forces cause the laterally flexible tires to generate increased slip angles. These angles, averaged at the front and rear, can be accommodated, with simplifying but reasonable assumptions, within an expanded ‘dynamic Ackermann’ equation. Importantly, the cornering-force-induced slip angles reduce turn radii and assist vehicle handling. Although not immediately self-evident, rear tires also steer via these angles – but passively.
Automobile steering mechanisms are generally designed to operate in the sector between low-speed Ackermann and parallel steer. Sports cars tend to be configured toward parallel steer while sedans tend toward pure Ackermann. Both vehicle platforms would normally have tire toe-in for stability.
Race cars, on the other hand, might utilize parallel steer, or even reverse or anti-Ackermann, with toe-out for maximizing tire scrub and steering. The supposition follows: if steered wheels remain parallel during cornering, or operate with reverse Ackermann, the outside tire-wheel assembly, already more heavily loaded due to centrifugal force, would suffer additional lateral scrubbing, which would further improve handling. Rapid tread wear is the penalty. Conversely, vehicles featuring either rear-wheel steering systems (such as forklifts) or four-wheel steer are apt to remain relegated to niche applications. Both steering modes tend toward oversteer at moderate to higher speeds, but operate well at low speeds when manoeuvrability is required.
Steering systems such as rack-and-pinion mechanisms conforming to variations in early four-bar trapezoidal linkages began in earnest with the development of motorized road transport, and improvements continue today. Rightfully or wrongfully, Ackermann’s name survives with these newer systems, not Darwin’s or Lankensperger’s – two centuries after publication of his eponymous British patent.
Ackermann Steering Geometry
Steering geometry is one of the many tools at a race car designer’s disposal to ensure the car extracts maximum performance from all four tyres. In this Tech Explained article, we will cover the origins and purpose of what is known as Ackermann Steering geometry and how its variations can affect tyre performance across a vehicle’s operating range.
Defining Ackermann Steering
Consider a low-speed cornering manoeuvre, where all tyres are in pure rolling condition, and there is no vehicle sliding present. As the vehicle travels along a curved path, all four tyres follow unique trajectories around a shared turn centre, as defined by the blue arcs in Figure 1.

Figure 1: Simplified depiction of Ackermann Steering configuration
The different curvature radii mean that to avoid sliding, the steering geometry must steer the inside front tyre at a larger angle than the outside front. Ackermann Steering refers to the geometric configuration that allows both front wheels to be steered at the appropriate angle to avoid tyre sliding.
For a given turn radius R, wheelbase L, and track width T, engineers calculate the required front steering angles (δ_(f,in) and δ_(f,out)) with the following expressions:

The difference in front-wheel steer angle as a function of the input steer angle is known as Dynamic Toe. If the vehicle dimensions are known, it is possible to construct a curve of the desired toe change for the full range of expected turn radii, such as the example in Figure 2.

Figure 2: Ackermann Steering configuration for a sample vehicle
The tighter the desired vehicle turn radius, the larger the difference in steer angles required. Ackermann Steering geometry is a practical measure to avoid sliding tyres while in the pit lane or parking on the street. The picture gets much more complicated once the vehicle is at speed.
Incorporating Slip Angles
A vehicle navigating a curved path at speed requires centripetal force provided by the tyres’ lateral force capacity to maintain its trajectory. The centripetal force occurs when the tyre assumes a slip angle.
The subsequent difference between the tyre’s heading and the contact patch’s orientation shifts the turn centre of the vehicle forward, as depicted in Figure 3.
Figure 3: Effect of tyre slip angle on vehicle turn centre

If a tyre has a slip angle, the lateral sliding velocity component present is greater than zero.
For this reason, the goal is to fine-tune the sliding conditions of each tyre to optimise total performance, rather than try to avoid tyre slip entirely.
The key to unlocking this performance comes from understanding the relationship between vertical load and lateral force capacity in tyres.
Figure 4 displays the lateral force vs slip angle relationship for an Indy Lights Tyre across a range of vertical loads.

Figure 4: Lateral force vs slip angle curves for a Cooper Tires Indy Lights 2017 Front Tyre
The higher the vertical load on the tyre, the greater peak lateral force it can produce. At higher vertical loads, the peak lateral force arrives at a higher slip angle. This trend is expected but not necessarily present in all tyres and may depend on compound or construction.
The relationship between vertical load and peak slip angle is known as the Line of Peaks. Characterising the Line of Peaks is essential due to the onset of lateral load transfer during a cornering manoeuvre, transferring vertical load from the inside tyres to the outside tyres.
It is critical to make sure both tyres operate at their peak slip angles simultaneously to maximise performance. In the case of the Indy Lights tyre, this means that the more heavily loaded outside tyre should be at a higher slip angle than the inside tyre. Steering the outside tyre more than the inside for a given steering wheel input achieves this.
The result is the exact opposite of Ackermann Steering and is known as reverse Ackermann or anti-Ackermann. Many race cars fitted with Anti-Ackermann exploit the peak operating conditions of the individual tyres.
Designing for Ackermann
The Ackermann level in a vehicle steering geometry is represented as a percentage, where 100% Ackermann means the difference in steer angle between the inside and outside tyre matches the geometric low-speed turn centre.
Most race cars do not run 100% Ackermann or 100% Anti-Ackermann. Instead, fine-tuning their solution somewhere in between to meet their specific design goals and expected operating conditions.
There are a few critical considerations for a designer to make when selecting a steering geometry for a race car. Designers must understand the speed profile and track characteristics where the car will be racing.
The slower and tighter the track is, the more critical it becomes to employ Ackermann to help navigate hairpins and other tight corners where geometry dominates all else. While a Formula One car navigating a 200m radius cornering may benefit handsomely from Anti-Ackermann, a similar setup would severely hamper a Formula Student vehicle navigating a 5m radius hairpin.
An example of Anti-Ackermann employed on a Red Bull F1 Car is shown in figure 5.
Figure 5: Example of Anti-Ackermann employed on a Red Bull F1 Car (source: apexspeed.com)
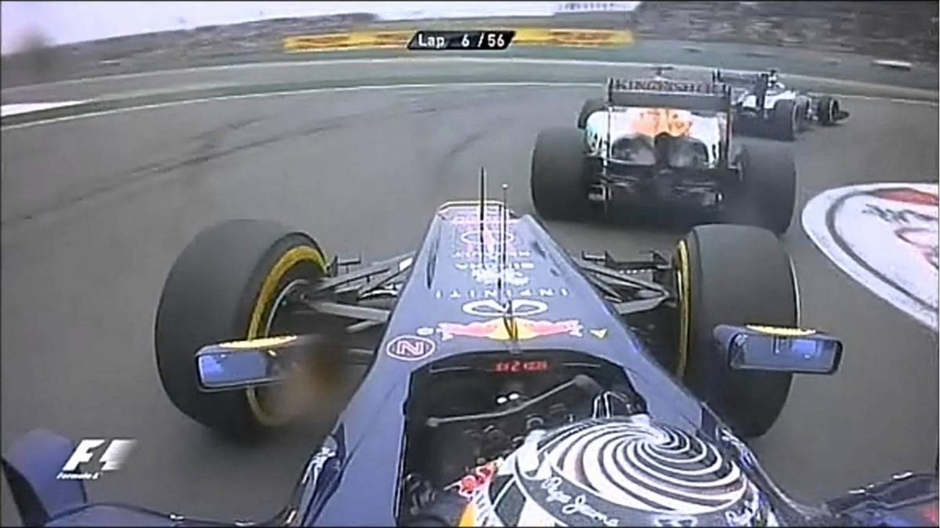
Designers must use the vehicle and track characteristics to predict the vertical loads on all four tyres throughout a lap. Fundamental factors can include weight, ride height, lateral load transfer distribution and downforce levels, and the complexity of analysis may depend on the information available.
A close approximation of vertical loads on all corners can combine with Line of Peaks information extracted from tyre data analysis to understand the peak slip angles for both front tyres on every turn. Designers can use this information to construct a target dynamic toe curve like the one shown in Figure 2.
In many cases, packaging and kinematic constraints may make it impossible to create a steering geometry that can match this target curve for all track corners. The designer will have to decide where they are willing to compromise performance.
Lastly, it is essential to remember that Ackermann is not the only way to adjust individual tyre slip angles. Bump steer can be incorporated kinematically to cause additional steer angle from suspension travel, which engineers can exploit when a vehicle rolls into a corner.
Also, no suspension components are purely rigid, and compliance in the links can affect the tyres’ steered angle in a corner. Suppose these factors are well understood and integrated into the suspension system.
In that case, it can help eliminate the compromises discussed above, but if they are ignored or misunderstood, it can lead to unpredictable cornering behaviour and performance losses.
Comentários