O2 Sensor Working
- Rohit Chaubal
- Aug 18, 2023
- 12 min read
O2 Sensor Working
The oxygen sensor is an essential component on engines using three-way catalytic converters to reduce exhaust pollution. It uses ceramic sensitive elements to measure the oxygen potential in the exhaust duct of the car. There are two kinds of oxygen sensors in practical application: zirconia oxygen sensor and titania oxygen sensor.
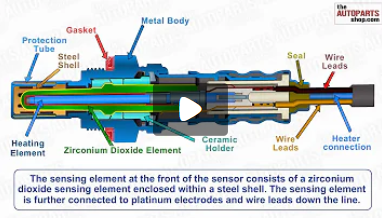
I Working Principle
The oxygen sensor is a standard configuration on the car. It uses ceramic sensitive elements to measure the oxygen potential in the exhaust duct of the car. The corresponding oxygen concentration can be calculated based on the chemical equilibrium principle to monitor and control the air-fuel ratio, ensuring product quality and the exhaust gas emission is up-to-standard. The oxygen sensor is widely used in the atmosphere control of the furnaces for coal combustion, oil combustion, and gas combustion.
It is currently the best combustion atmosphere measurement method, which has a simple structure and rapid response speed, and it’s very easy to maintain and use. Using the oxygen sensor to measure and control the combustion atmosphere can not only stabilize and improve product quality but also shorten the production cycle and save energy.
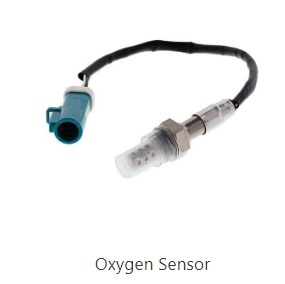
The zirconia in the oxygen sensor of a car acts like an electrolyte, which is similar to that of the dry battery. The basic working principle is: under certain conditions, the difference in oxygen concentration between the inside and outside of zirconia is used to generate a potential difference, and the greater the concentration difference, the greater the potential difference.
The oxygen content in the atmosphere is 21%. The exhaust gas after the combustion of the gas mixture does not actually contain oxygen, while the exhaust gas generated after the combustion of the lean mixture or resulting from the bad ignition contains more oxygen, but it is still less than that in the atmosphere.
Under high temperature and platinum catalyzing, oxygen ions with negative charges are adsorbed on the inner and outer surfaces of the zirconia sleeve. Because there is more oxygen in the atmosphere than in the exhaust gas, the side connected to the atmosphere absorbs more negative ions than the side connected to the exhaust gas, and the concentration difference between the two sides generates an electromotive force.
When the oxygen concentration on the exhaust side of the casing is low, a high voltage (0.6 to 1 V) is generated between the electrodes of the oxygen sensor. This voltage signal is sent to the ECU for amplification. Generally, the ECU regards the high voltage signal as a rich mixture and the low voltage signal as a lean mixture. According to the voltage signal of the oxygen sensor, the computer dilutes or enriches the mixture as close as possible to the theoretical optimal air-fuel ratio of 14.7:1. Therefore, the oxygen sensor is a key sensor for electronically controlled fuel metering.
Oxygen sensors can only output voltage at high temperatures (end temperature > 300°C) and react fastest to the change of the mixed gas at about 800°C. This characteristic will change greatly at low temperatures.
II Function
In order to obtain a high exhaust purification rate, and reduce the components of (CO)carbon monoxide, (HC)hydrocarbons, and (NOx)nitrogen oxides in the exhaust gas, we must use a three-way catalyst converter. However, in order to effectively use the three-way catalyst converter, the air-fuel ratio must be accurately controlled to close to the theoretical air-fuel ratio. The catalyst converter is usually installed between the exhaust manifold and the muffler.

Gasoline engine catalyst efficiency function of air-fuel ratio
The voltage output of the oxygen sensor has a sudden change near the theoretical air-fuel ratio (14.7:1). This characteristic is used to detect the oxygen concentration in the exhaust gas, which is fed back to the computer to control the air-fuel ratio.
When the actual air-fuel ratio becomes higher, the oxygen concentration in the exhaust gas increases and the oxygen sensor notifies the ECU of the lean state (small electromotive force: 0 volts). When the air-fuel ratio is lower than the theoretical air-fuel ratio, the oxygen concentration in the exhaust gas is reduced, and the status of the oxygen sensor (large electromotive force: 1 volt) is notified to the computer (ECU).
The ECU determines whether the air-fuel ratio is low or high based on the difference in electromotive force from the oxygen sensor, and controls the duration of fuel injection accordingly. However, if the oxygen sensor breaks down and the output electromotive force is abnormal, the (ECU) computer cannot accurately control the air-fuel ratio. Therefore, the oxygen sensor can also compensate for the error of the air-fuel ratio caused by the wear of the mechanical and other parts of the electronic fuel injection(EFI) system. It can be said to be the only "smart" sensor in the EFI system.
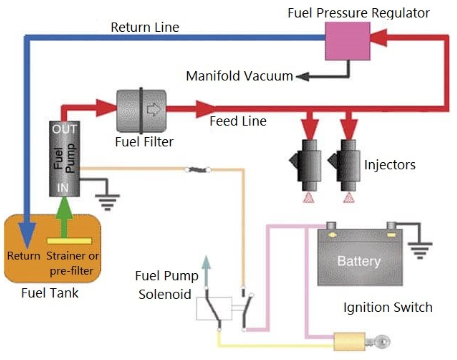
Working of EFI(electronic fuel injection system)
The sensor can also measure whether the oxygen in the exhaust gas of the engine is excessive after combustion, that is, the oxygen content. It converts the oxygen content into a voltage signal to the engine computer to enable the engine to achieve closed-loop control with an excess air factor as the target. Moreover, by doing this, it can ensure the three-way catalytic converter has the maximum conversion efficiency for the three pollutants of hydrocarbons (HC), carbon monoxide (CO), and nitrogen oxides (NOX) in the exhaust gas, and converts and purifies the emission pollutants to the greatest extent.
III Classification
There are two kinds of oxygen sensors in practical application: zirconia oxygen sensor and titania oxygen sensor. It can also be divided into types of single-lead, double-lead, and three-lead. Usually, the zirconia oxygen sensor is the single-lead type, the titanium oxygen sensor is the double-lead, and the heated zirconia oxygen sensor belongs to the three-lead type. In principle, these 3 types of oxygen sensors can not replace each other.
1. Zirconia Oxygen Sensor
(1) Structure of Zirconia Oxygen Sensor
The zirconia oxygen sensor is mainly composed of zirconia (ZrO2) and sheath. There are two types of zirconia oxygen sensor: heated type and unheated type. The heated oxygen sensor has a heating rod in the middle of the zirconia tube. The zirconia tube is made of the ceramic body and fixed in a sleeve with mounting threads.
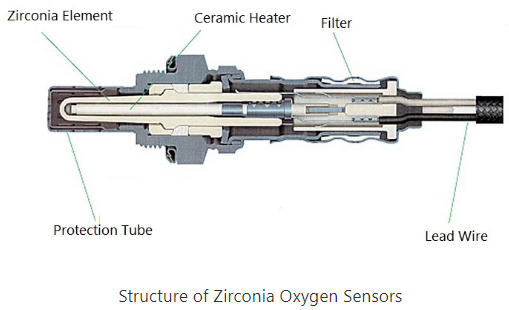
The inner and outer surfaces of the zirconia tube are covered with a layer of the porous platinum film as an electrode. In order to prevent the exhaust gas from corroding the platinum film, the platinum film layer on the outer surface of the zirconia tube is covered with a porous ceramic layer. There is a protective sleeve with notches or holes on it. The terminal of the oxygen sensor has a metal sheath with a hole on it to connect the inner surface of the zirconia tube with the air. The platinum electrode on the inner surface of the zirconia tube is led out through an insulating sleeve.
(2) Features of Zirconia Oxygen Sensor
Advantages: simple structure, quick response, easy maintenance, convenient use, accurate measurement. Using this sensor to measure and control the combustion atmosphere can not only stabilize and improve product quality, but also shorten the production cycle and save energy.
Disadvantages: The characteristics above can only be fully reflected when the temperature is high (about 600 ℃). At low temperatures, these characteristics will change greatly.
2. Titanium Oxygen Sensor
(1) Working Principle of Titanium Oxygen Sensor
Compared with the zirconia oxygen sensor that generates a voltage signal, the titanium oxygen sensor(TiO2) uses the change in resistance to determine the oxygen content. Above a certain temperature, the combination of titanium and oxygen is weak. When there is little oxygen, the oxygen must be abandoned, so a low-resistance oxide semiconductor is generated for the lack of oxygen.
Conversely, if there is a lot of oxygen, a high resistance state is formed. Just like the water temperature sensor, there is a change in resistance. At this time, as long as a reference voltage is supplied, the temperature of the cooling water can be known from the voltage.

The schematic function of a TiO2 sensor
(2) Features of Titanium Oxygen Sensor
The working principle of the titanium oxygen sensor is very different from that of the zirconia oxygen sensor. It is made by using the characteristics that the conductivity of porous conductor TiO2 changes with the change of oxygen content in the exhaust gas, so it is also called resistance oxygen sensor.
This kind of sensor has a simple structure, small size and low cost, but when working at 300℃-900℃, the resistance value changes greatly with temperature. Usually, another solid TiO2 conductor is used as a temperature compensation to improve accuracy.
IV Common Faults of Oxygen Sensor
1. Oxygen Sensor Poisoning
Oxygen sensor poisoning is a failure that often occurs and is difficult to prevent. Especially for cars that often use leaded gasoline, even new oxygen sensors can only work for thousands of kilometers. If there is only mild lead poisoning, we can replace it with a box of lead-free gasoline, the lead on the surface of the oxygen sensor can be eliminated and restore normal operation. However, due to the excessively high exhaust gas temperature, lead intrudes into its interior, hindering the diffusion of oxygen ions, thus making the oxygen sensor ineffective. At this time, it can only be replaced.
In addition, silicon poisoning of oxygen sensors is also a common occurrence. Generally speaking, the silicon dioxide is generated after the combustion of the silicon compound contained in gasoline and lubricating oil, and the silicone gas is emitted when the silicone rubber gasket is used improperly. Both of them will invalidate the oxygen sensor, so we should use good-quality fuel and lubricating oil. Besides, rubber gaskets should be properly selected and installed during repairs. Do not apply solvents and anti-sticking agents other than those specified by the manufacturer to the sensor.

Sensor Poisoning
2. Carbon Deposit
Due to the poor combustion of the engine, carbon deposits are formed on the surface of the oxygen sensor. Besides, deposits such as oil or dust inside the oxygen sensor will block the outside air from entering the oxygen sensor, causing the signal output by the oxygen sensor to be inaccurate, and the ECU cannot timely correct the air-fuel ratio. The typical signs of carbon deposits are mainly the increase in fuel consumption and the obvious increase in emission concentration. At this time, if the sediment is removed, the sensor will resume normal work.
3. Ceramic Chipping
The ceramic of the oxygen sensor is hard and brittle, and it can be broken and damaged when hit with a hard object or blown with strong airflow. Therefore, special care should be taken and we should replace it in time if problems are found.
4. Burned Resistance Wire
For the heated oxygen sensor, if the resistance wire of the heater is ablated, it is difficult for the sensor to reach the normal working temperature and it will lose its function.
5. Disconnected Internal Circuit
6. Clutter
V Analysis of Clutter
1. Causes
The clutter of the oxygen sensor signal is usually caused by the following reasons:
(1) Bad ignition of the cylinder.
(2) System design, such as different channel lengths of intake pipes
(3) The expansion of system design problems caused by the aging of engines and components(the expansion of different intake pipe channel length caused by the imbalance cylinder pressure)
2. Bad ignition Influence
The glitches and clutter on the waveform under bad ignition are caused by those single combustion times or series of combustion events that are incompletely burned or not burned at all, which makes the effective oxidation part being used in the cylinder, and the remaining excess oxygen goes to the exhaust pipe through the oxygen sensor. When the sensor finds that the composition of the oxygen in the exhaust gas changes, it quickly generates a low pressure or glitch. A series of these high-frequency glitches form something we called "clutter".
3. Different types of Bad Ignition
(1) Bad ignition caused by the firing system (for example, damaged spark plugs, high-voltage power lines, distributor traps, ignition coils, or primary ignition problems that only affect a single cylinder or a pair of cylinders). Usually, ignition oscilloscope can be used to identify and eliminate these faults;
(2) Bad ignition caused by the rich mixture sent to the cylinder, which makes the air-fuel ratio of the given dangerous mixture is about 13:1;
(3) Bad ignition caused by the lean mixture sent to the cylinder. The given dangerous mixture air-fuel ratio turns to 17:1;
(4) Bad ignition caused by cylinder pressure, which is due to mechanical problems (Eg burned valve, broken or worn piston ring, worn cam, stuck valve, etc.);. The cylinder pressure reduces the pressure of the fuel-air mixture before ignition and the heat generated is not enough. This hinders combustion and increases the oxygen content in the exhaust gas.
(5) There is vacuum leakage in one cylinder or several cylinders. This can be determined by adding propane to the suspected vacuum leaking area (intake impeller, intake manifold gasket, vacuum tube, etc.). When the signal increases due to the addition of propane, the spike disappears. When the vacuum leakage related to one cylinder or several cylinders causes the mixture to enter the cylinder to exceed 17:1, bad ignition occurs.
(6) Bad ignition caused by an unbalanced injection of the fuel injection nozzles. It only occurs in multi-point jet engines, if the actual amount of oil injected by each fuel injection nozzle is too high or too little(clogged or stuck,) the rich oil or lean mixture of one cylinder will cause bad ignition. When the air-fuel ratio of the gas mixture in a cylinder or several cylinders exceeds 17:1, a bad ignition is generated by the lean mixture. When it is lower than 13:1, a bad ignition is generated by the thick mixture. This is the bad ignition caused by the imbalance of the fuel injection nozzle.
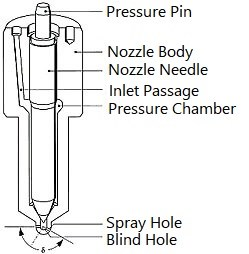
VI Troubleshooting of Oxygen Sensor
The troubleshooting methods of the oxygen sensor are as follows:
1. Measure the Resistance
Use an ohmmeter to measure the resistance between the terminals of the oxygen sensor socket (heating resistor). The colors of the two adjacent wires from the heating resistor are the same, which is easy to distinguish. Cold resistance is about 4 ohms. (The oxygen sensor has four wires arranged in a row, one pair is connected, which is the resistor end; the other pair is not connected, which is the signal output end)
If there is an open circuit or the resistance is not within the normal range, the oxygen sensor needs to be replaced; if the resistance value is normal, then proceed to the next step.
2. Measure the Power Supply Voltage
Turn on the ignition switch and measure the voltage between the terminals of the oxygen sensor plug (harness side) corresponding to the heating resistor end, which should be the battery voltage. If the voltage is low or none, repair the circuit from the oxygen sensor plug to the injection relay.
3. Measure the Insulation to the Ground
Use an ohmmeter to measure the resistance between the heater and the housing, which should be ∞.
If there is a passage, replace the oxygen sensor. If there is no passage, proceed to the next step.
4. Measure the Signal Voltage
(1) Turn off the ignition switch and disconnect the 4-pin connector on the oxygen sensor;
(2) Lead the 12V power supply of the battery to the resistance heating end of the oxygen sensor. This method needs to make a pair of connectors with wires. After connecting, start the engine and measure the voltage at the signal output terminal after 2 minutes.
If you think that this method is not operable, you can start the engine directly. After 2 minutes, unplug the four-core connector and quickly measure the voltage of the signal terminal on the oxygen sensor. However, the core of the oxygen sensor will cool down after the heating resistance is disconnected from the power supply for a long time, and the measurement error will increase.
In the idle state after starting the engine, this output voltage should be very low according to the above working principle. At this time, if we increase the accelerator, and there will be a voltage output at this moment, which is related to the rate of change of the accelerator(if the accelerator is stable, the voltage disappears immediately). The faster the change, the greater the voltage, which can reach the maximum value of 0.9V. If it is a pointer meter, due to inertia and damping factors, this voltage can only be 0.8V. (Considering the response time of the digital meter, the engine cannot be measured with a digital meter, otherwise, the error is very large)
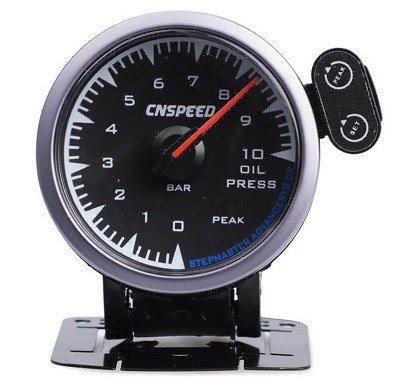
A Pointer Meter
If there is no voltage output of the oxygen sensor, the voltage value is unchanged, the voltage rise or drop is very small, and the voltage change is very slow, it means that there is a problem with the sensing element of the oxygen sensor. At this time, consider cleaning the oxygen sensor as follows:
Remove the oxygen sensor, add excess hydrochloric acid to the 5-10% ferric trichloride solution. This ratio depends on the condition of the sensor head surface.
Soak the oxygen sensor in the solution, take it out after 10-15 minutes, and rinse it with water. After washing, not only the four holes around it should be unobstructed, but the carrier inside should be white when we see it from the bottom. If the cleaning is not ideal, continue this work until you can see the white carrier.
After rinsing with water, install the sensor and repeat the fourth step of measurement. Generally speaking, as long as the internal ceramic body is not cracked, and the heating resistor is not open, the oxygen sensor can resume normal operation after the cleaning.
Frequently Asked Questions
1.What happens when an oxygen sensor goes bad?
If your vehicle has a bad oxygen sensor, it could run irregularly or sound rough when it idles. A faulty oxygen sensor can impact your engine's timing, combustion intervals, and other essential functions. You could also notice stalling or slow acceleration.
2.Can you drive with a bad oxygen sensor?
Yes, you can drive with a bad oxygen sensor if you can still start your engine and feel little difficulty driving. But don't leave it alone for over a couple of days, as it might cause safety problems and lead to the malfunction of other parts of your vehicle.
3.How much does it cost to fix an O2 sensor?
A brand new replacement oxygen sensor can cost you from $20 to $100, depending on the make and year of your car. Taking your car to a mechanic to fix the issue can cost up to $250.
4.How much is a oxygen sensor?
If you decide to do the repairs, the cost to replace the oxygen sensor yourself can be between $20-$94, depending on the brand and type of sensor you buy. To have the repairs done by a mechanic the price can be anywhere between $113 to $478 for parts and labor.
5.What causes an oxygen sensor to fail?
O2 sensor failures can be caused by various contaminants that enter the exhaust. These include silicates from internal engine coolant leaks (due to a leaky head gasket or a crack in a cylinder wall or combustion chamber) and phosphorus from excessive oil consumption (due to worn rings or valve guides).

Comments