Octane Number
- Rohit Chaubal
- Aug 3, 2023
- 6 min read
An octane rating, or octane number, is a standard measure of the performance of an engine fuel. The higher the octane number, the more compression the fuel can withstand before detonating (igniting). In broad terms, fuels with a higher octane rating are used in high-performance gasoline engines that require higher compression ratios. In contrast, fuels with lower octane numbers (but higher cetane numbers) are ideal for diesel engines, because diesel engines (also referred to as compression-ignition engines) do not compress the fuel, but rather compress only air and then inject fuel into the air which was heated by compression. Gasoline engines rely on ignition of air and fuel compressed together as a mixture, which is ignited at the end of the compression stroke using spark plugs. Therefore, high compressibility of the fuel matters mainly for gasoline engines. Use of gasoline with lower octane numbers may lead to the problem of engine knocking. [1]
Octane number, also known as Antiknock rating, is one of the most important characteristics of gasoline. Octane number is a measure of a gasoline’s ability to avoid knocking as it burns in the cylinder’s combustion chamber. ‘Knocking’ is caused by the uncontrolled auto-ignition of unburned fuel (called end-gas) brought into contact with elevated temperatures and pressures in the cylinder.
Engine knock has a high pitched, metallic rapping noise. Using an octane lower than what the engine is designed for may cause a loss of fuel economy and vehicle performance. Prolonged use of low octane gasoline can result in engine damage.
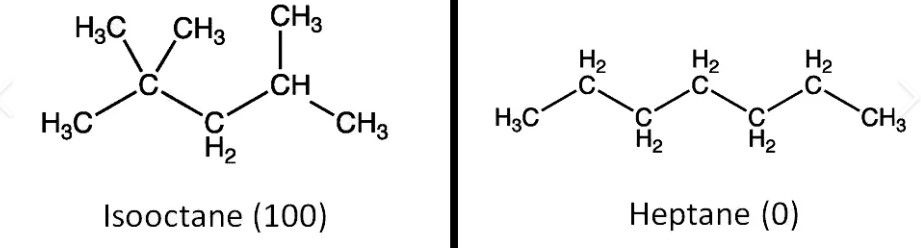
Normal Combustion vs. Detonation
Normal combustion is the burning of a fuel and air mixture charge in the combustion chamber. During the combustion, fuel should burn in a steady, even fashion, originating at the spark plug and progressing across the chamber. Detonation is the spontaneous combustion of the end-gas (remaining fuel/air mixture) in the chamber.
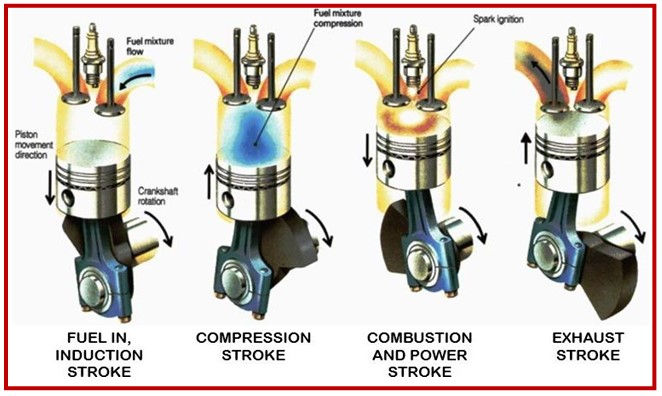
The initial combustion at the spark plug should be followed by a normal combustion burn. Unburned end gas with insufficient octane, under increasing pressure and heat from the normal progressive burning process spontaneously combusts. Detonation causes a high pressure spike and force in the combustion chamber. It causes the engine to ring, or resonate, much as if it were hit by a hammer.

Think of yourself jumping on a trampoline with a second person. If you come down right as the other person is bouncing up, your legs will get shocked as you no longer get a smooth bounce off of the trampoline. When your car "knocks" (fires early because the octane is too low) something similar is happening as shockwaves push against the pistons at the wrong time.
A = Application
Antiknock Index (average of RON and MON or (R+M)/2) is the accepted method of relating RON and MON to road performance in vehicles. U.S. Federal Trade Commission (FTC) regulations require a label on each service station pump showing the minimum (R+M)/2 value of the fuel dispensed. For fuels sold in the United States, regular grade is typically 87 (R+M)/2 (often slightly lower at high altitudes), midgrade is typically 89, and premium is typically 91 or higher. A consumer can match the (R+M)/2 value specified in the owner’s manual with the value on the pump. There is no benefit if the octane is higher than what the engine needs.
M = Methods
The antiknock rating of a spark-ignition engine fuel is measured in single-cylinder laboratory engines. Two methods have been standardized to measure octanes:
· ASTM D2699 Test Method for Research Octane Number of Spark-Ignition Engine Fuel
· ASTM D2700 Test Method for Motor Octane Number of Spark-Ignition EngineFuel
Another method used for quality control in fuel blending is:
· ASTM D2885 Test Method for Research and Motor Method Octane Ratings Using On-Line Analyzers.
S = Scope
Research Octane Number (R.O.N.) correlates with commercial automotive spark-ignition engine antiknock performance under mild conditions of operation (cruising with a light load).
Motor Octane Number (M.O.N) correlates with commercial automotive spark-ignition engine antiknock performance under severe conditions of operation (pulling away from a stop light or going up a hill with a heavy load).
Antiknock Index (AKI) or Road Octane = 0.5 x Research Octane Number + 0.5 x Motor Octane Number
R.O.N. and M.O.N. are used by engine manufacturers, petroleum refiners and marketers, and in commerce as a primary specification measurement related to the matching of fuels and engines.

P = Procedure Notes
ASTM Standard: The Octane Number (O.N.) of a spark-ignition engine fuel is determined using a standard test engine and operating conditions to compare its knock characteristic with those of Primary Reference Fuel (PRF) blends of known Octane Number. Compression ratio and fuel-air ratio are adjusted to produce standard Knock Intensity (K.I.) for the sample fuel, as measured by a specific electronic detonation measurement system. A standard Knock Intensity guide table relates engine Compression Ratio to Octane Number. The fuel-air ratio for the sample fuel and each of the PRF blends is adjusted to maximize Knock Intensity for each fuel. The procedure applies for ratings within the range from 80 to 100 Octane Number.
Simply Stated: Cars with higher compression engines deliver more horsepower but require higher octane. These single-cylinder engine test procedures use a variable compression-ratio engine. Using a diaphragm pickup in the cylinder, the knock intensity is captured and sent to the detonation meter where it is converted to electrical energy and sent to the engine’s knockmeter.
The Motor (MON) method operates at a higher speed and inlet mixture temperature than the Research method (RON). There are three procedures that may be used, bracketing, compression ratio or dynamic/falling level.
The procedures relate the knocking characteristics of a test fuel to standard fuels, which are blends of two pure hydrocarbons: isooctane (resists knocking) and n-heptane (readily knocks). These blends are called primary reference fuels. By definition, the octane number of isooctane is 100, and the octane number of n-heptane is 0.
Bracketing Procedure ASTM Standard: The engine is calibrated to operate at standard K.I. in accordance with the guide table. The fuel-air ratio of the sample fuel is adjusted to maximize the K.I., and then the cylinder height is adjusted so that standard K.I. is achieved. Without changing cylinder height, two PRFs are selected such that, at their fuel-air ratio for maximum K.I., one knocks harder (higher K.I.) and the other softer (lower K.I.) than the sample fuel. The sample fuel O.N. is calculated by interpolation in proportion to the differences in average K.I. readings. Simply Stated: The reference fuels are forced to knock and the knocking intensity in the cylinder is converted to electrical energy that is sent to the engine’s knockmeter. The unknown fuel is then forced to knock and the knockmeter number is used to interpolate the octane result.
RON example using the bracketing method:
94.0 Octane Reference fuel (94% Isooctane + 6% Heptane) knocks at 44 on the knockmeter.
92.0 Octane Reference fuel (92% Isooctane + 8% Heptane) knocks at 56 on the knockmeter. The unknown fuel knocks at 50 on the knockmeter and interpolating calculates to 93.0.
((HIGH REFERENCE OCTANE - LOW REFERENCE OCTANE) x (LOW REFERENCE METER - UNKNOWN METER)) / (LOW REFERENCE METER - HIGH REFERENCE METER)) + LOW REFERENCE OCTANE
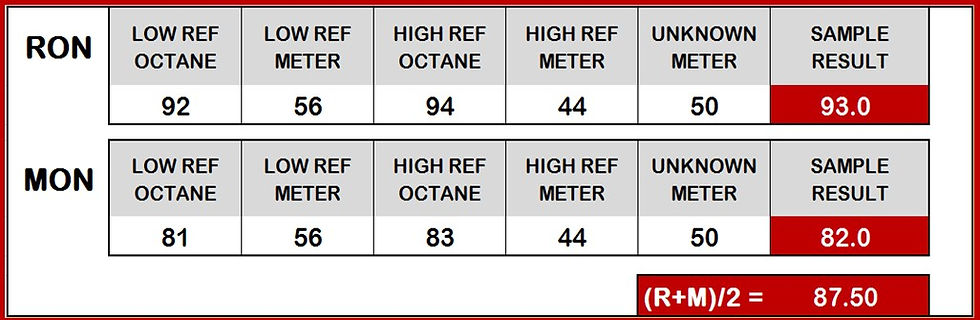
Compression Ratio (C.R.) Procedure ASTM Standard: A calibration is performed to establish standard K.I. using the cylinder height specified by the guide table for the O.N. of the selected PRF. The fuel-air ratio of the sample fuel is adjusted to maximize the K.I. under equilibrium conditions; the cylinder height is adjusted so that standard K.I. is achieved. The cylinder height reading for the sample fuel is converted directly to O.N. using the guide table. Simply Stated: The engine is lined out on the reference fuel blend by manually adjusting the carburetor level to maximum knock and adjusting the cylinder head height as listed on the guide table. Once stable, the detonation meter is adjusted until the knockmeter is at 50. The unknown fuel is then run and maximum knock obtained by manually adjusting the carburetor level. The cylinder head height is then adjusted until the knockmeter is at 50. The cylinder height reading is found on the guide table and equates to the fuel’s octane number. Falling Level, Dynamic Fuel Level Procedure ASTM Standard: The fuel-air ratio for maximum knock intensity for sample and reference fuels is determined using the falling level technique that changes carburetor fuel level from a high or rich mixture condition to a low or lean mixture condition, at a constant rate, causing knock intensity to rise to a maximum and then decrease, thus permitting observation of the maximum knockmeter reading. Simply Stated: The fuel bowls do not have a float. The level in the bowl goes down as the engine burns the fuel. The engine will go from low knock, to peak knock, and back to low knock. Compares peak knock difference between the unknown fuel and reference blends. The knockmeter readings are
used to interpolate the octane result similar to what is done with bracketing. This method is used for computerized lab automated semi-attended testing.
E = Equivalents
ASTM D2699 = IP 237, Test Method for Research Octane Number of Spark Ignition Engine Fuel, and ASTM D2700 = IP 236, Test Method for Motor Octane Number of Spark-Ignition Engine Fuel
ASTM D2885 = IP 360, Test Method for Research and Motor Method Octane Ratings Using On-Line Analyzers.
C= Cause & Effect
Using too low an octane may cause a loss of fuel economy and vehicle performance. With newer vehicles with computerized knock sensors, damage due to knocking is not as significant as it was in older vehicles. Higher compression engines require higher octane. The loss of power and the damage to an engine due to knocking is generally not significant until the knock intensity becomes severe and prolonged.
Thanking You
@ CR's Autozeal
댓글