Temperature Sensors
- Rohit Chaubal
- Aug 18, 2023
- 10 min read
Temperature Sensors
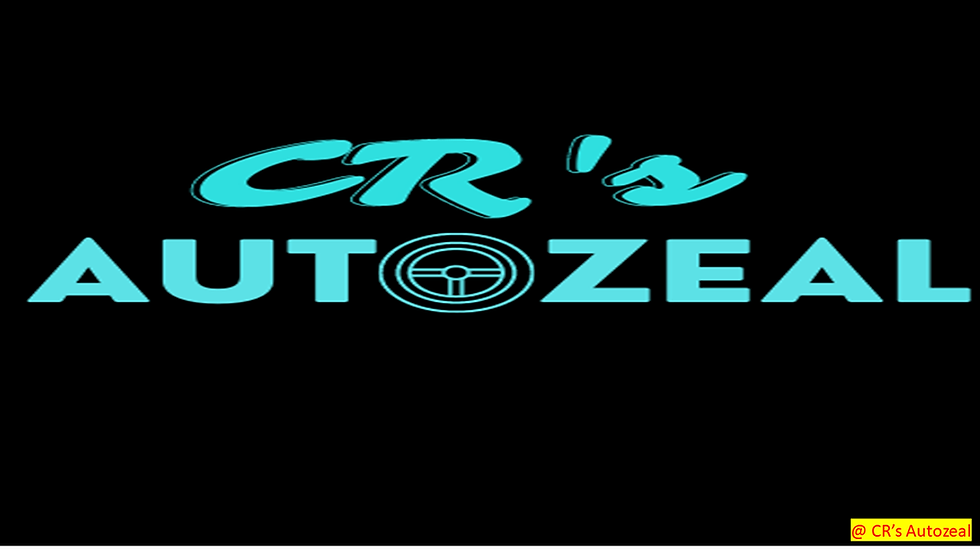
Introduction
The temperature sensor refers to a sensor that can sense the temperature and convert it into a usable output signal, which is the core part of the temperature measuring instrument. It's divided into 5 types and each type has unique working principles. Besides, some factors need to be noticed in the installation and using process. For the temperature sensor can accurately measure the ambient temperature, it's widely used in various fields and provide convenience for people's production and daily lives.

I Classification
The temperature sensor is one of the most frequently used sensors, which is widely used in computers, automobiles, kitchen appliances, air conditioners, and household thermostats. The five common types of temperature sensors include thermocouples, Thermistors, RTDs (Resistance Temperature Detectors), analog thermometer IC, and digital thermometer IC.
1. Thermocouple
The combination of two different conductors or semiconductors is called a thermocouple. The thermoelectric potential EAB (T, T0) is composed of the contact potential and the temperature difference potential. Contact potential is generated by two different conductors or semiconductors at the contact point, which is related to the property of the two and the temperature at the contact point.
When two different conductors or semiconductors A and B are connected to each other to form a loop, as long as the temperature at the two nodes is different, there will be a current in the circuit. The temperature at one end is T, which is called the working end, while that at the other end is TO, which is a free end, and the electromotive force at this moment is called thermal electromotive force. The electromotive force is generated due to different temperatures, which is named the Seebeck effect.
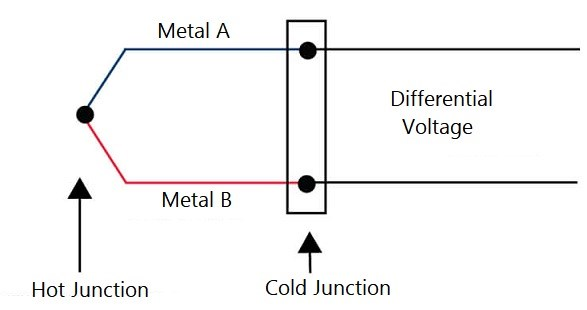
Fundamental Thermocouple
2. Thermistor
The thermistor is a type of sensing element. The resistance value of the thermistor will change with the temperature. Unlike the fixed resistor, it is a type of variable resistor that is widely used in various electronic components. And different from resistance thermometers that use pure metals, thermistors are usually made of ceramics or polymers.
The positive temperature coefficient thermistor has a larger resistance value at a higher temperature, and under the same condition, the negative temperature coefficient thermistor has a lower resistance value. The thermistor usually has higher accuracy in a limited temperature range, usually from -90 ℃ to 130 ℃.
3. Resistance Temperature Detector (RTD)
Resistance temperature detectors (RTD) measures the temperature according to the rule that the resistance of the conductor changes with temperature.
The temperature-sensing element of resistance thermometers are commonly made of metal wires as platinum and copper, and at low temperatures, carbon, germanium, and rhodium iron are often used for the element.
Because they are almost made of platinum, we often call them platinum resistance thermometers. The precision platinum resistance thermometer is the most accurate thermometer, which covers a temperature range of about 14 to 903K, and its error can be as low as 1/10,000 degrees Celsius. Besides, it can reproduce the international practical temperature scale.

Construction of RTD
4. Analog Thermometer IC
Usually, an analog low-voltage temperature sensor is applied to replace the thermistors and fixed resistors in the voltage divider circuit, such as TMP36 of Analog Devices.
As shown in the figure, compared to the thermistor, the output voltage provided by this analog IC is almost linear. In the temperature range from -40 to + 125°C, the slope is 10mV/°C, with the accuracy of ±2°C.
5. Digital Thermometer IC
Digital thermometers are more complicated, but they are very accurate. Besides, they can simplify the overall design as the analog-to-digital conversion occurs inside the thermometer IC, rather than with a separate device like a microcontroller.
For example, DS18B20 of Maxim Integrated has an accuracy of ±0.5°C and a temperature range of -55°C to + 125°C. Moreover, some digital ICs can collect energy from their data lines, thereby only allowing two lines (ie. data/power and ground wire) for connection.
II Working Principle
Different types of temperature sensors have different working principles:
1. Thermocouple Sensing
Thermocouples consist of two metal wires of different materials welded together at the ends. By measuring the ambient temperature of the unheated part, we can obtain the temperature of the heating point.
Thermocouples with different materials are used in different temperature ranges, and their sensitivities are also different. The sensitivity refers to the variation of the output potential difference when the temperature of the heating point changes by 1°C. For most thermocouples made by metallic materials, this value is between 5 and 40 microvolts /°C.
Since the sensitivity of the thermocouple temperature sensor has no connection with the thickness of the material, thin materials can also be used for production. And because the metal material has good ductility, thermocouples have a high response speed to measure the process of rapid changes.
2. Resistance Sensing
As the temperature changes, the resistance value of the metal also changes. And for different metals, the resistance value changes differently with the temperature, which can be directly used as the output signal.
Resistance changes in 2 different ways:
● Positive temperature coefficient
temperature increases → resistance increases
Temperature decreases → resistance decreases
● Negative temperature coefficient
temperature increases → resistance decreases
Temperature decreases → resistance increases

3. Principle of Metal Expansion
The metal will extend after the ambient temperature changes, and the sensor can convert this response to different signals.
4. Bimetallic Sheets
The bimetallic sheet is composed of two pieces of metal with different expansion coefficients. As the temperature changes, the material A expands more than the other metal, causing the metal sheet to bend. The curvature can be converted into an output signal.
5. Deformation Curve of Liquid and Gas
When the temperature changes, the volume of the liquid and gas will also change accordingly. Various devices such as potentiometer and baffles can convert this expansion change into a position change, producing an output variation.
III Selection of Temperature Sensor in Industry
Temperature is a very critical parameter in industrial production, as it has direct effects on product quality, equipment, and personal safety.
In the selection of temperature sensors, we should not only consider high measurement accuracy, large range, and high automation, various factors such as the specific process in industrial production, the property of the medium, and the economical efficiency should also be taken into account.
The main principle is:
● The operation method meets the observation needs of the measurement personnel,
● Convenient for daily inspection and maintenance
● The upper and lower measurement temperature limits of the test instrument should be greater than the temperature fluctuation range of the measured medium.
● The measurement accuracy meets the technical requirements of the production process
● Economical
Let's discuss in detail from 4 aspects:
1. Choose by Usage
If only the local display is required, we can choose liquid glass, bimetal, and pressure thermometer. If we want to be alarmed when the measured temperature is close to the limit value, a thermometer with additional warming devices should be selected. And If a long-distance display is required, a thermistor, thermocouple, or temperature transmitter will be the best choice.
2. Temperature Range of the Medium
To choose a suitable temperature sensor, the temperature of the medium to be measured is an important criterion.
If measuring normal temperature, we can choose thermocouple, resistance, pressure, and bimetal thermometer.
The indicating liquid of the organic-liquid glass thermometer is red, which is good for reading, but this thermometer can not connect points with charges. Thus, when the temperature of the medium is below 100 ℃ and there is no need to send a signal, the organic liquid glass thermometer is preferred. The bimetal thermometer has a clear scale without mercury and is vibration-proof, which is often applied when the temperature of the medium is lower than 300 ℃.
The table below shows the selection of temperature sensor under different temperature ranges:

3. Measurement Accuracy
If the measurement accuracy is very high, we can use a platinum resistance thermometer, platinum-rhodium platinum thermocouple, or platinum rhodium-platinum rhodium thermocouple. If the measurement accuracy is not very high, the copper resistance thermometer and nickel chromium-nickel silicon thermocouple are preferred.
4. Chemical Properties of the Medium
Most thermocouples are stable in oxidizing or neutral mediums, but they can not work for a long time in reducing medium, which is the same for platinum resistance thermometers.
When the temperature reaches 100 ℃, copper resistance thermometers and thermistors are easily oxidized. To deal with this, protective sleeves with appropriate materials should be installed according to the chemical property of the measured medium.
For thermocouples, if the temperature is below 600℃, medium carbon steel, copper, lead, etc. can be selected for bushings. When the temperature is below 1000℃, austenite stainless steel is usually used for its hot-corrosion resistance. In addition, we must pay attention to the compatible use of secondary instruments, thermocouple compensating wires, and temperature compensators at the free end. During the installation, the accuracy of the test must be ensured to benefit the maintenance and calibration of the instrument and avoid the lag of temperature measurement.
IV Precautions for Use
When we install and using the temperature sensor, the following matters should be noted to obtain the best measurement results(taking thermocouple as the discussing object):
1. Improper Installation
Improper installation means that the installation location and insertion depth of the thermocouple can not reflect the true temperature of the furnace. Here are the specific explanations.
● The thermocouple should not be installed too close to the door and the heating place, and the insertion depth should be at least 8 to 10 times the diameter of the protective tube.
● The gap between the protective tube and the furnace wall hole of the thermocouple should be filled with thermal insulating materials like refractory mortar or asbestos ropes, or the hot and cold air cross-ventilation affects the accuracy of temperature measurement.
IV Precautions for Use
When we install and using the temperature sensor, the following matters should be noted to obtain the best measurement results(taking thermocouple as the discussing object):
1. Improper Installation
Improper installation means that the installation location and insertion depth of the thermocouple can not reflect the true temperature of the furnace. Here are the specific explanations.
● The thermocouple should not be installed too close to the door and the heating place, and the insertion depth should be at least 8 to 10 times the diameter of the protective tube.
● The gap between the protective tube and the furnace wall hole of the thermocouple should be filled with thermal insulating materials like refractory mortar or asbestos ropes, or the hot and cold air cross-ventilation affects the accuracy of temperature measurement.

● If the cold end of the thermocouple is too close to the furnace, its temperature will exceed 100 ℃
● The thermocouple should not be installed in the strong magnetic field and electric field, so the thermocouple and power cable should not be installed in the same conduit to avoid errors caused by interference
● It cannot be installed in the area where the medium rarely flows. When we measure the gas temperature in the tube with a thermocouple, the thermocouple must be installed against the flow direction of the gas and be fully in contact with it.
2. Insulation Fault
If there is too much dirt or salt slag on the protective tube and the stain plates, it will cause defective insulation between the thermocouple and the furnace wall, which is more serious at high temperatures. Moreover, it will cause the loss of thermoelectric potential and introduce interference, resulting in errors of hundreds of degrees Celsius.
3. Thermal Inertia
Due to the thermal inertia of the thermocouple, the indicated value of the instrument will lag behind the change of the measured temperature, which is particularly prominent during the quick measurements. Therefore, thermocouples with a thin hot end and protective tube of smaller diameters should be the first choice. The protection tube can even be removed if the environment permits.
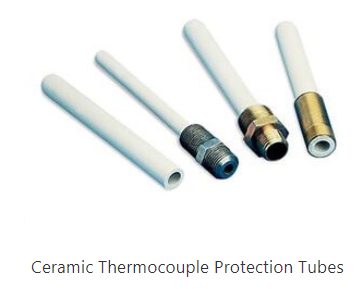
Due to the measurement lag, the temperature fluctuation amplitude detected by the thermocouple is smaller than the actual amplitude in the furnace. The larger the measuring lag, the smaller the fluctuation amplitude of the thermocouple, and the greater the difference from the actual furnace temperature. When we measure or control the temperature with a thermocouple of a large time constant, although the temperature fluctuation displayed by the sensor is little, the actual fluctuation may be great.
In order to measure the temperature accurately, a thermocouple with a small-time constant should be applied. The time constant is inversely proportional to the heat transfer coefficient and proportional to the diameter of the thermocouple hot end, the density of the material, and the specific heat. Therefore, the most effective method to reduce the time constant is to minimize the size of the hot end.
n actual application, the protective tube of the thermocouple usually has a thin wall and small diameter, and the material is of good thermal conductivity. In more precise measurements, the thermocouple without protective sleeves is used, but it is easily damaged, so we should replace it in time.
4. Thermal Resistance
At high temperatures, if there is a layer of coal ash on the protective tube and the dust is attached to it, the thermal resistance will increase and hinder the heat conduction. At this time, the indicating value of the temperature is lower than the true value. Therefore, the outside of the protective tube should be kept clean to reduce errors.
V Application Fields
The temperature sensor is the most commonly used among all the sensors. The modern temperature sensor has a small shape, which makes it widely used in various fields of production practice and provides convenience for people's lives. They're used in the following areas:
1. Sensing Application
The thermal conversion method of temperature sensors is often used to measure physical quantities, such as flow rate, radiation, gas pressure and type, humidity, thermochemical reaction, etc... These measured values are all output as electrical signals.
2. Biomedical Domain
Special temperature sensors are often applied for biomedical applications. These temperature sensors have low power consumption, long-term stability, and high reliability, with an accuracy of less than 0.1℃ between 32℃ C and 44℃
3. Space Application
'
Thermistors and silicon PN junctions have been used for temperature measurement in space. Using discrete analog and digital interface circuits to read the temperature from sensing elements is high-cost, which is not suitable for micro/nano satellites. The intelligent temperature sensor with the digital output can be used in satellite design in the future and can transmit digital information compatible with the microprocessor.
4. Industrial Application
'
Integrated temperature sensors can be applied in automation and microbe thermal detection. And intelligent temperature sensors with powerful digital interfaces and communication systems can meet the requirements of low cost, long-term stability, and reliability.
5. Consumer Products
Many low-cost integrated temperature sensors and transmitters have been used in consumer products such as washing machines, refrigerators, and air conditioners. The sensors used in these products are usually low-cost without external parts and the measurement accuracy can reach 0.5 ℃ from 20℃ to 100 ℃.
Frequently Asked Questions
1.What are the temperature sensors? A temperature sensor is an electronic device that measures the temperature of its environment and converts the input data into electronic data to record, monitor, or signal temperature changes. There are many different types of temperature sensors. Non-contact temperature sensors are usually infrared (IR) sensors.
2.What is temperature sensor and its types? There are four types of temperature sensors that are most commonly used in modern-day electronics: thermocouples, RTDs (resistance temperature detectors), thermistors, and semiconductor based integrated circuits (IC).
3.How do temperature sensors work? The basic principle of working of the temperature sensors is the voltage across the diode terminals. If the voltage increases, the temperature also rises, followed by a voltage drop between the transistor terminals of base and emitter in a diode.
4.Which is the best temperature sensor? An NTC thermistor is able to achieve the highest accuracy of the basic sensor types within the -50 °C to 250 °C range. Accuracy ranges from 0.05 to 1.5 with high long-term stability, depending upon the type of sensor and packaging used. NTC thermistors also offer superior responsiveness, on the order 0.12 to 10 s.
5.What are the three ways that temperature sensors can be tested? Testing the Engine Coolant Temperature by Visual Inspection. Testing the ECT Using a Multimeter. Testing the ECT Sensor Using a Scan Tool.
Comments